CYCOGS® Hybrid Snake Arms - Continuum Robot Arms
The
CYCOGS® Company wishes to inform our web site visitors, with some valuable AI Robotics information.
Please note, the
CYCOGS® Company
owns and or controls the copyright of all material in this website.
The
content of the “Education”
portion of this web site is still under the
CYCOGS® Company registered copyright protection.
Obtain some information about Hybrid Snake Arms and the
CYCOGS® brand Snarm™ - Snake Arm and Platform.
In
Robotics,
there are many mechanical Robotic arms types and modes of movement.
For traditional Robotic Arms, many arms are of the
X-Y Gantry style.
Next in Robot Arm popularity, we have the typical
Industrial Multi-Axis Robot Arms.
The typical Multiaxis Industrial Robot Arms include the more recent style of
Deltoid Robot Arms making inroads, and then we have the other Robotic Arm types.
Industrial Robot Arms provide a highly repeatable, positional accuracy and high load ratings.
This is in part due to their rigidity and fixed mountings. Industrial Robot Arms’ rigidity
possesses advantages for such tasks as precise welding and manufacturing.
In Mobile Robot usage, the Robot can be found moving as well as operating off a pliable surface
like padded carpeting. Soft surfaces will undermine the precise,
repeatable positioning capacities of a rigid industrial Robot arm, possibly rendering its use as inaccurate and unnecessary.
For a Mobile Robot, industrial arms are just too large and heavy.
A Robotic Snake Arm is a long, cylindrical-shaped, mechanical Robotic arm comprised of many segments
on a flexible backbone support.
The Snake Arm Robot is able to move in ways similar or reminiscent of a snake’s motion or elephant trunk movements.
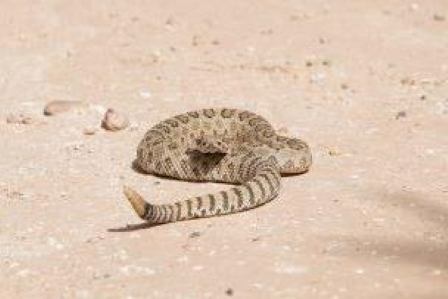
The snake arm may also be called a continuum robot, flexible tube structure, tensor arm, flexible frame, flexible positioning appendage,
flexible body, multi-articulated manipulator, serpentine arm and snaky or snake-like arms.
The flexible Snake Arm is a Robotic "Arm" utilizing many elements such as movable links,
ribs or plates connected in series and moved by a mechanism like wires or cables.
The Robot arm actuation methods typically employ a
flexible power transmission
ability needed as the arm flexes to create a pivoting motion or action between the elements.
Such interconnecting actuators may include motor driven cables, wires, tendons, and control lines, as well as various electromechanical,
hydraulic, pneumatic, and mechanical mechanisms like gears, pistons, cams and other actuating systems,
Generally, each arm element is grouped into a controlled arm segment, where that segment as a whole is moved.
Typically, the distance between two edges of the ribs or plates is changed and when multiplied by many elements,
the combined displacements causes the arm to move.
Arm segments can be moved by shortening one side and lengthening the other side of a segment to induce movement.
The arm actuators are typically grouped or segmented to move a subset series of plates or elements.
To move or position an arm, a portion or segment of the arm, such as the first 1/5 segment of the arms actuators are then activated.
This would be followed by a second group of actuators, wires or cables that connect to the next 1/5 segment of the arm, and so on.
One segment typically uses at least four actuators, one per quadrant, for such movement directions as
Up, Down, Right, and Left.
Most conventional snake arms or continuum robot arms are a round tube-like appendage, separately attached to the arms’ actuators and controls.
The actuators and controls are usually separate from the arm sections to reduce the arm dead weight and to allow more room for the controls.
Consequently, typical snake arms resemble a box with a flexible hose projecting from the middle of one side.
Furthermore, flexible Snake Arms or continuum robot arms may implement various types of joints to maintain a desired shape and alignment,
for example, universal joints, springs, ball joints, sockets and elastomers and the like.
Snake arm Robots or continuum robots are typically built with a small outer diameter compared to its overall length,
with each element member of a segment movable in two rotational
Degrees of Freedom (DoF).
If you multiply the number of elements by two, you can get an approximate
cumulative DoF count.
It is routine for the count to reach 20 - 50 DoF.
The large DoF count may also be classified as a
continuum Robot arm,
depending on the spacing and flexibility of each element, and its element to element connection.
The snake arm is capable of moving in translation, rotation, and to move in a spiral or coil like fashion,
as well as to move left, right, up, or down by using the CYCOGS® rotary platform and the "snake" robot arm.
The rotary platform can be rotated in any direction or heading,
and is also capable of
continuous 360 - degree rotations.
The hybrid Robot snake arm moving to touch the chassis of the Robot.
The convoluted snake arm can reach any location inside its working envelope.
The working envelope typically is a circular light bulb or tear drop shape, as the arms can flex in any direction.
Some dead spots will occur at the conventional snakes’ arm’s minimum bend radius zones.
Some
dead zone coverage is possible if the arm is long enough to curl around itself.
Previous snake arm designs do not address the Mobile Robot requirements of compact arm storage.
A massive working area and the ability to produce 360 degrees of rotational freedom for arm tasks while mounted in a Robot.
To expand this working envelope, the whole flexible snake arm system would need to be reoriented.
The CYCOGS® Company developed a rotating platform for mounting and integrating the Snake Arm.
By locating the Snake Arm on this rotary platform, the working envelope is vastly expanded.
Furthermore, the snake arms actuators and controls can be located and integrated on this rotating platform.
The
CYCOGS® Company platform for the snake robot arm for Mobile Robots can provide
360 degrees of continuous platform rotation for rotating one or more arms about a central axis with no arm obstructions.
The arm’s platform can rotate in any direction, system speed or acceleration.
This hybrid system additionally allows stationary arm positioning coupled with the robot platform rotations.
If the Robot body rotates, the arms can follow the work in progress with access to all areas around the Robot in its
available work envelope.
Furthermore, the platform facilitates arm storage where the Robot snake arm can curl around the platform for a
compact storage mode, within the boundaries of a circular Robot.
The
CYCOGS® Company named the
intelligent advanced hybrid snake arm and platform, the “
Snarm™.
”
The CYCOGS® companies advanced intelligent hybrid Robotic Snake Arm and rotary platform system
(Snarm™) integrated the snake arm and platform into a unique system.
The Snake Arm is attached to the computer-controlled rotary platform, allowing the snake arm orientation to be rotated at any speed,
direction or acceleration the system is capable of reaching.
This provides an expanded movement space, called the working envelope.
The envelope expansion is accomplished, by attaching a snake arm robot tangentially,
or located near the outer circumference to the rotatable platform.
The Snarm
™ hybrid Robot snake arm and platform, showing possible elevation movements and the spherical or donut-like
works space or envelope of a Mobile Robot.
A compliant or "springy" Robot arm is preferred when operating in such environments near humans.
The
CYCOGS® Company advanced intelligent hybrid Snake Arm and Platform Robot system
(Snarm
™) solves the storage, working envelope, obstacle avoidance and compliance issues.
The Snarm
™ can navigate or flow around obstacles and is compliant for use around humans and other animals.
The compliance feature allows the arm to operate with more safely.
Collisions with objects are minimized and are softened by
"giving" upon contact. This feature is sometimes considered, "compliant behavior."
Maximum force may not be exerted immediately, giving the arm controls time to react to unexpected events.
This illustration on the left shows the
CYCOGS® Company hybrid Robot snake arm and platform
(Snarm
™) parked, fully retracted and coiled up at zero degrees.
The snake arm and platform are then shown fully extended in
tangential extension on the right.
This illustration shows the Snarm
™ beginning to uncoil.
The middle illustration shows the platform with the snake arm partially uncoiled.
And on the right is the snake arm and platform partially
uncoiled in extension
with an end effector clear of the chassis;
This illustration on the left shows the Snarm
™ snake arm and platform with a bump or
loop arm extension.
The middle illustration shows the Snarm
™ in a loop or hook position.
The right illustration shows a maximum arm extension example.
This illustration shows a Mobile Robot employing two of the hybrid Robot snake arm platforms being used in a medical or nursing
type application for such tasks as lifting and moving patients or equipment.
The snake arms can pick up a patient and transfer the patient from a bed onto a gurney.
In addition, the snake arms can ease nurse workloads and perform some
patient repetitive physical therapy.
The bump or loop arm extension can additionally be used to carry a box or an injured patient.
A Mobile Robot so equipped
can act as a nurse’s assistant.
The combination of the CYCOGS® Company Snarm’s snake arm and the rotary platform offers a
potentially unlimited variety of curves, positions and orientation combinations as well as end effector positioning options.
This illustration shows the working envelope of a Mobile Robot with a Snarm™ hybrid snake arm.
The Snarm
™ snake arm is capable of performing work within the donut-shaped or
spherical working envelope region located concentrically about the Robot or platform axis.
The snake arm is equally able to traverse a convoluted path,
such as flowing around obstacles to place the end effector at a given location.
The snake arm rotary platform can cooperate as the snake arm extends, like from the circular coiled storage position.
One type of extension of the snake arm represents a
tangential translating arm extension,
operating much like extending a retractable tape measure.
To perform the CYCOGS® Company Snarm™ tangential translating arm extension,
from the stored position, the snake arm or continuum robot first straightens out the end segment in an uncurling fashion.
Then the snake arm and the rotary platform work together, to match
the uncurling rate of the snake arm with the rotary rotation
rate of the rotary platform to produce
a
linear extension of the snake arm until the snake arm fully extended.
The snake arm can be retracted by performing the identical procedure in reverse.
With this type of operation, the snake arm can be extended just enough to carry out the required work.
Another type of CYCOGS® brand Snarm™ extension is uncoiling
from the circular coiled storage position.
This caused the Snarm
™ to uncoil the snake arm in a spiral like extension, basically an
expanding swinging arc.
The rotary platform does not need to rotate. The Snarm
™ uncoiling operations occur as the coiled snake arm starts to move outward.
The individual arm segments can all act at the same time to perform the uncoiling operation.
The snake arm is uncoiled and extended from the rotary platform past the outer robot body.
The rotation of the rotary platform is not required, but may be implemented as an arm navigation aid to thread the snake arm around an obstacle.
Another type of the CYCOGS® brand Snarm™ arm extension is from the circular coiled storage position,
where the snake arm can extend a segment outside the boundaries of the Robot or platform, like a bump or loop.
The
bump or loop arm extension can be used to carry a box or an injured patient.
Noted on the illustration below, left side.
In addition, the arm segments can
move objects by pushing on them,
much like we humans use our elbows to push open a door with our hands full.
The CYCOGS® brand Snarm™ end effector capable of performing
automated tool or sensor changes.
For example, if such tools are located within its working area or in the robot’s body, the arm can reach and exchange end effector components.
End effectors like claws, hands, etc. can be positioned in the large volume of the
workspace envelope.
Several companies manufacture Robot arm end effectors such as, for example, claws, pinchers and hands.
Automated end effector changing systems allowing the end effector to exchange, for example, a claw for a hand.
Some tasks will require different mated end effector appendages, like a brush for painting, or a gripper to open a door.
The ability to adapt end effector tooling and sensors are enhanced with the combination of the snake arm rotary platform.
The expanded work envelope allows more access to
tools and sensor storage locations.
Such storage locations can be located within or on the body of the robot or external to the robot, in various locations like a tool crib.
Such exchangeable tools and sensors may include claws, pinchers, hooks, hands, drills, brushes, rollers, cameras, laser scanners, etc.
The robot arm end effector can employ a camera embedded inside the snake arm for aligning and coupling with various tools and sensors
as well as for guiding the installed tool to its task.
Numerous tasks will require the ability for the arm end effector to change its tooling and sensors.
The typical snake arm / continuum robot or even a typical industrial Robot arm, when used with the rotary platform may require a "skin."
Such a "
robotic skin" may be fashioned out of a flexible material and may include such features as a
stiffener for the Robot arm, a sensor and control network and compliant padding.
The compliant padding minimizes any point sources of pressure from mechanical contact, which is useful for tasks such as,
for example, carrying a dog or lifting an injured patient.
The
CYCOGS® brand Snarm
™ skin can be equipped and operated as a
flexible sensor network for detecting contact with another object,
such as with a force or weight detector,
tactile sensors and hair like sensors.
These sensors enhance movements of the snake arm in close proximity to objects without substantial physical contact.
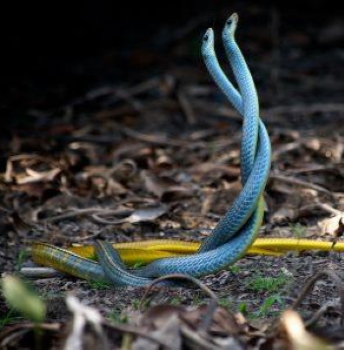
Such multiple Snarm
™ hybrid robot arm systems can be configured in a stacked configuration, a back-to-back configuration.
The
CYCOGS® brand Snarm
™ hybrid Robot arm system can track with a modular sensor ring
(shown in Red) as it rotates around the Robot’s body while sharing the sensor ring's
data between the primary computer and other subsystems to plan and perform work with the Snarm
™ snake arms.
The
CYCOGS® Company developed
the rotary arm platform to enable advanced snake arm Robotic movements and capabilities for our Mobile Robots.
For further details on the
CYCOGS® brand Snarm
™,
please see the Snarm product page here.
For a story about the
CYCOGS® brand Snarm
™,
CYCOGS please see its story here.
Learn more about AI Robotics with the
CYCOGS® Company
Education and Classroom topics.
The
CYCOGS® Company Articles Robot Tech Series:
Contact: Send questions and comments about the Snake Arm Robotics by CYCOGS web site to the
CYCOGS® Contact.