CYCOGS AI Robotics Stories
Find some interesting
CYCOGS® Company Mobile Robotics and Artificial Intelligence
Stories of Interest.
The
CYCOGS®
Company owns and or controls the copyright of all material in this website.
The content of the “Stories” portion of this web site is still under registered copyright protection.
CYCOGS AI Robotics stories and information are facts not fiction.
The CYCOGS Story.
The
CYCOGS® Company arose from the desire to achieve a more capable world and help our fellow humans by employing AI Robotics technology.
We at the
CYCOGS® Company have always found AI Robotics technology appealing, with hardware, software and integrated control systems particularly fascinating.
While many people experience life while ignoring technology, few routinely and continuously study it.
You may find yourself in a technology disadvantage if your usage and exposure are merely using a couple of apps on your smart phone and hanging out watching sports.
If you follow this trend, new technology developments will become “
scary magic.”
The
CYCOGS® Company has positioned itself on a long-term business plan.
We have seen many AI Robotics companies come and go, and we feel terrible when the great ideas they had are lost or damaged in order to reach the next quarters bottom lines.
Much of the technology and uniqueness of these companies is then lost.
Some have criticized the
CYCOGS® Company for its rate of progress, but we are still here!
We still strive to implement technology to help our fellow humans to construct a better world, plus generate increased profits.
Our skill sets developed into robotic computer control and automation of real-world devices. It was just a matter of time for the technical convergence to arrive.
The Big Robot Story.
The CYCOGS® Company robotics influenced its direction from the need and desire to manufacture and sell an extremely capable mobile robot system.
We decided to make this an indoor robot with exceptional capacity.
One of the early
CYCOGS® Company decisions was on mobility. How to make the robot move and be a
"
useful mobile robot."
Walking may be fine for some, but it is inefficient, with much “infrastructure” dedicated to walking and not falling down.
Walking weight carrying capacity was a major limitation.
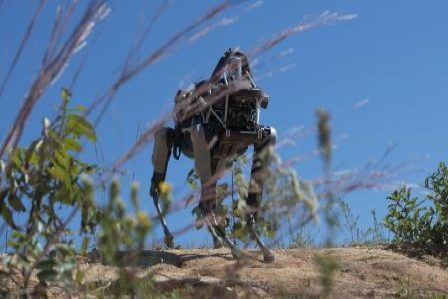
Tracked mobility movement was too bulky and inefficient and lacks the ability to perform precise movements.
This left us with wheels.
Wheels have been wielded in the past for thousands of years and will be used for thousands of years more in the future, for many legitimate reasons.
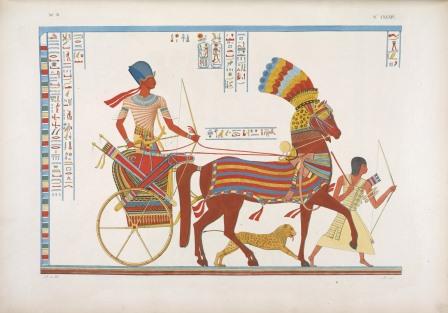
The CYCOGS® Company is developing robotics that can perform substantial work, is mobile, and is able to lift and move things,
similar to a typical human’s capability.
Unmistakably a 50-pound plastic robot with more in common with toys was out.
We decided to design and build a Medium Sized Robot (MSR
™).
The next crucial issue was doorways.
Being able to transverse doorways then limited the maximum physical size. The long car like designs was finished.
You have to go up. Exploiting this as a guideline, the most suitable shape was a tall round robot that provided the most volume for its size and environment.
This unfortunately forced the use of robotic arms into a complex problem.
For further details on the
CYCOGS® brand
Medium sized robot (MSR™),
please see the MSR product page here.
The Hi2WAM™ story.
With the
CYCOGS® Company robot defined in bold strokes; how can we make its mobility requirements a reality?
Differential Mobility
could work by employing two large wheels, always tippy, rocking from the front to the rear.
Not particularly stable, and would result in high floor loading on those two wheels.
Synchronous Mobility
is nice, using three wheels to define a plane.
Almost perfect!
But using synchronous robot mobility includes a limitation. Synchronous mobile designs cannot move in certain ways.
Synchronous mobility equipped robots cannot pivot on a wheel, nor rotate its body.
If you have a robotic arm picking up some item, with no ability to orient the wheel geometry for best weight distribution, your robot may be tip-over prone.
Mechanum wheels
are not terribly effective in this case also, too much maintenance, vibration and floor wear/damage, and the list goes on.
The solution to this problem is to use the
wheeled holonomic mobility
drive type and its enhanced movement abilities.
Holonomic mobility can mimic the motion capabilities of the differential and synchronous drives, plus more!
Holonomic mobility type vehicles are able to move in any way the robot needs.
This mobility ability also enables a robotic arm equipped mobile robot to rotate its body, placing a wheel under/closer to the load.
Such abilities allow the tip over issue to be managed.
Directly using a three wheeled holonomic mobile robot represents a great solution to this mobility problem.
We wanted to keep the robots floor loading weight lower to minimize the buildings floor wear and avoid damage.
You can drop the per-wheel floor loading in half if you double the number of wheels!
With the three wheel assemblies equally spaced in the robot, doubling the wheel count furnishes you with six wheels, and if driven,
six-wheel drive!
Using six wheels additionally allows the use of smaller diameter wheels, and a resulting smaller vehicle volume, compared to larger two and three-wheel designs.
But CYCOGS had a balance and a collision problem.
Our tall robot needed to lean or correct its stance for uneven flooring and floor transitions, especially in doorways.
And when the robot arms lift a heavy object, a means to
shift the center of gravity (CG) would be helpful.
Plus, we wanted to
measure the load on each wheel for tip and balance monitoring.
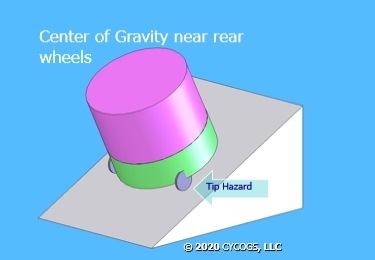
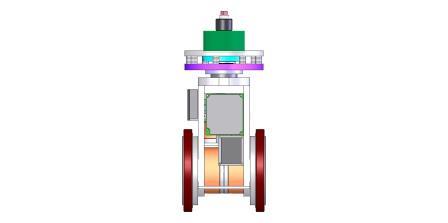
The CYCOGS® Company solution was to design an active suspension system to adjust the height of each wheel pair.
We directly have height control, with an active suspension!
We know we could fabricate it into an integrated base, but that base would be complex and routine maintenance would be slow and problematic.
As a result, we designed each wheel pair as a removable wheel assembly module and gave the holonomic wheel assembly some local intelligence and control and called it the
CYCOGS
brand
Hi2WAM™ .
This
4 - DoF
design opened up the use for the Hi2WAM
™ in other designs.
Design choices like one Hi2WAM
™ equipped vehicles ranging up too many wheeled devices.
If you consider a lengthy item to transport, and you want to keep it evenly supported?
Use as many Hi2WAM’s as it takes.
For further details on the
CYCOGS brand Hi2WAM
™,
please see the Hi2WAM product page here.
For a tutorial covering the
CYCOGS brand Hi2WAM
™,
please see its education page here.
The WA™ Story.
When the
CYCOGS® Company developed the Hi2WAM
™,
we knew the wheeled form factor needed a compact motor and compact gear reduction.
Nothing like what we needed was in existence.
The
CYCOGS® Company had to develop our own wheel drive system.
We needed the dual wheels as close together as possible, yet independently driven.
Sounds easy, merely take an electric motor, some gears, bearings and a wheel and you are all set.
Attempt that without a
compact short axial length design!
Some may think, “just use a Harmonic gear reduction and a short motor.” Nice thought, if you don’t mind ending up being 10-14 inches wide.
We did it in
under 4” (about 95mm)!
To accomplish this short length,
CYCOGS developed a novel, redundant, hypocyclic gear reduction that is embedded in the wheel hub and used a unique iron core-less motor.
This is a
CYCOGS® Company exclusive item
just like the Hi2WAM
™ it was developed for.
When we developed the Hi2WAM™,
selling the sub compact wheel assembly was not on our radar screens.
But demand was there, and it is directly a
CYCOGS® brand product, the
Wheel Assembly (WA™).
The SNARM™ Story.
With the robotic mobility issues under control, the
CYCOGS® Company pondered what about the robotic arms?
We needed a robot arm capacity to manipulate objects, lift excessive loads, and have a large compliant working-envelope plus be able to fit on or into our robot.
Furthermore, we required two robotic arms.
With our tall robot, where would the arms go?
The
CYCOGS® Company studied many robotic arm types in our quest. We started backwards from the goals and specifications we had outlined.
We knew we required two robotic arms, with useful load capacities, good arm speeds, compliance in human environments,
a huge working envelope and the desire to locate the arm in or about our mobile robot.
Once more, we could not locate anything that would work. No one has ever created robotic arms that would accommodate our needs.
So, back to the drawing boards.
Standard industrial arms have the capacity and speed issues sorted out.
But these arm types provided a terrible fit for our working envelope, power use, size and weight requirements.
Absolute arm repeatability is not much use as the mobile robot could be shifting on a carpet or moving across the floor or adjusting its attitude.
This mushiness in its environment diminished the advantage of fixed robotic arm repeatability and accuracy.
The
CYCOGS® Company had finalized plans on a good
Medium-Sized mobile Robot (MSR™)
with a cylindrical body.
The robot’s mobility was holonomic, so we could position the arms by rotating the body.
But if the arms are located on the outer perimeter of the mobile robot, the arms would be in the way.
With protruding robotic arms, the robot would be limited in its mobility in tight locations.
And the robots job requirements required the use of two arms at once, limits any fixed mounting locations.
We could develop a shorter robot and place the arms on the top.
Top mounted robotic arms would allow limited arm access if something was on the floor, and that nevertheless had the problem of using both arms at once for some tasks.
What to do?
We pondered what kind of mobile robot chassis would resolve this?
After much R&D,
CYCOGS developed a chassis with a lower power mobility section, a hollow central support “
column” and a
top electronics/control section.
Once we had the chassis design problem sorted out, our new chassis design enabled us to solve the arm problem using the two arms and the working envelope issues went away.
The result, the CYCOGS® Company developed the
hybrid-rotating snake arm platforms
located inside the robot!
With this robot design development, one type of robot arm fell into place.
The
multi-segmented snake arms!
Normally these snake arms are long and not at all suitable for storage or mobile robotics use. With our rotating platform, the arms simply curl up upon the rotating platform!
In this manner, the
arms can be stored inside the robot, no substantial parts sticking out!
The
CYCOGS® Company subsequently developed our own arm design
and realized we had the perfect force drive for it.
Our dual wheeled, Holonomic Wheel module
(Hi2WAM™)
uses
very compact redundant hypocyclic gear reduction drives used in the
Wheel Assembly (WA
™) and Orientation Drive.
We merely modified the wheel assembly/orientation drive for the snake arm gear reduction drives and created the
Compact Gear Motor drive (CGM™).
Now CYCOGS has an internally stored, dual-hybrid snake arm system, plus with a huge 365-degree floor to ceiling working envelope!
Additionally, the system is compliant and strong enough for
use around humans
like picking someone up off the floor and putting them into bed.
We at the
CYCOGS® Company, feel our Hybrid Snake Robot Arm is the
ultimate in robotic arm capabilities,
even better when coupled to a mobile robot!
We named it the
CYCOGS® brand
Snarm™!
For further details on the
CYCOGS® brand Snarm
™,
please see the Snarm product page here.
For a tutorial about the
CYCOGS® brand Snarm
™,
please see the Snarm education page here.
Our CGM™ Story.
We needed a compact motor and gear reduction to ensure the orientation of the dual wheels for steering purposes, as some movement types required absolute controlled movements,
and any floor slippage or obstacles could throw off the movements.
We had developed the
Orientation drive and the Wheel Assembly
(WA
™) for the Hi2WAM
™
and determined these designs minimal size and generous capacity was perfect for this orientation positioning.
The electric gear reduction drive was not infact a separate product yet.
As you may have read from the SNARM
™ story, we also needed a compact gear motor to move the segments of our snake arms.
Traditional gearing, including harmonic gearing was still too bulky, and with our compliant arms, absolute repeatability and zero backlash was not an issue.
We had developed a compact gear motor based off the WA
™ for orienting the Hi2WAM’s wheels, and found that with some modifications,
we could implement the same basic drive on the snake arm segments.
With an eye to utilizing common parts, we had created the
CYCOGS® brand
Compact Gear Motor (CGM™) product
now found in the Hi2WAM™
and
Snarm™ systems.
The SRing™ Story.
Many traditional robots have one, two or more video cameras that are ether fixed or have limited movement.
We pondered this
sensing problem.
CYCOGS has a very capable holonomic robot in the works that can move in any direction, had dual hybrid snake arms, and we wanted exceptional sensing capabilities.
With the
holonomic
ability to perform such motions as in a rotating translation “
Frisbee Glide”,
(think of putting a counter-rotating camera on a spinning flying Frisbee to watch its forward path) we had another problem.
We could throw a gazillion sensors all over its body to cover and sense every angle or decouple the sensors from the fixed body by
rotating the sensors.
Some sensors are inexpensive (cheap) and some are enormously expensive (IR cameras and LIDAR sensors)
and if we rotated the sensors, we had a means to expand a sensors
field of view (FoV).
Consequently, the
CYCOGS® Company developed a
rotating sensor platform!
This sensing capacity allows the robot to
perceive its environment
in any direction.
The sensors can be controllably positioned at any rotation angle and can be positioned to study an area of interest or a continuous rotating scan of a room.
We decided to use two sensor rings to keep track of the two
Snarm robot arms as they are capable of
independent movements.
The rotating sensor ring expands any sensors view, coverage and lowers the overall cost due to this “Sensor Magnification.”
This became the
CYCOGS® brand
Sensor Ring (Sring™) product.
This concludes the story of some of our design choices. We feel this is the best solution available. Stay tuned for more stories.
CYCOGS AI ROBOTICS Stories by and about
CYCOGS Mobile Robotics and Artificial Intelligence development.
The
CYCOGS® Company has other stories of Interest we will want to talk about.
When we are prepared, we will provide some decidedly engaging stories to include covering
AI-Robotics and
CYCOGS developments.
Contact: Send questions and comments about this web site to the
CYCOGS® Contact.